There is really just one worthwhile alternative to soldering when it comes to transferring A/C refrigerant, gas, fuel-oil, or very high-pressure water through soft copper or aluminum conduit. Flare fittings enable a strong mechanical joint that can sustain pressures in the range of 450–3000 psi, depending on the pressure rating of the materials being used, when soldering with an open flame could prove challenging or dangerous, a genuine risk when working with gas and oil lines.
Flare fittings consist of a threaded body with flared ends and a nut, and are typically made of brass or steel. They establish their extremely secure link by using a similar pipe Flaring tool. A unique tool is used to get that flared finish.
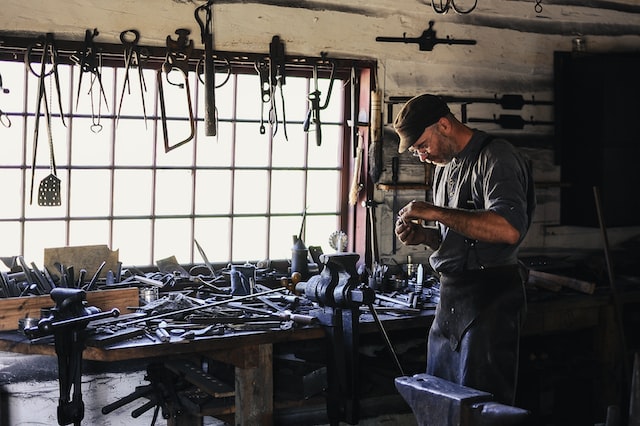
Tools for flaring pipes are fairly straightforward in both design and use. They are made up of two separate components: a flared cone attached to a yoke and a die block with openings for various pipe sizes. The soft metal is shaped into the fitting’s required 45° flare as the cone is forced into the pipe end.
Hacksaws and other cutting tools can result in an uneven cut or burrs, which can impair the flare, therefore cutting your copper or aluminum with a tube cutter will assure a clean cut.To get rid of any burrs and debris in and around the pipe end, use a deburring tool or an abrasive cloth.The tapered end of the flare nut should be pointing away from the end of the pipe that will be flared as you slide it onto the pipe. Before both ends of the pipe are flared, the nuts must be attached.Put the pipe in the die block’s matching hole. If the pipe end of your flare is flush with the block, everything should work out perfectly.
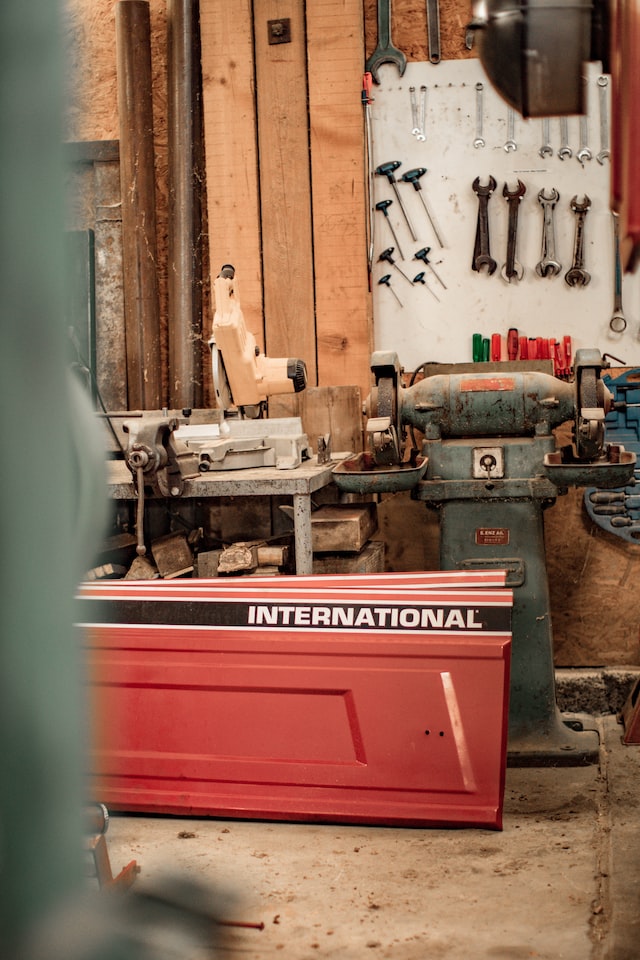
First, tighten the wingnut that is closest to the pipe.After that, tighten the outer wingnut.The yoke should hook or clamp into place on the underside of the die block when it is placed on the block.Place the cone so that it is directly above the pipe that needs to be flared. The cone can be moved toward the pipe by turning the handle.Continue spinning until there is no more room for the cone to be tightened in the pipe.Remove the yoke and pull the cone out.From the die block, remove the pipe. The freshly flared pipe end needs to be even and smooth.Verify it in relation to the fitting body to make sure the flare rests completely and uniformly on the fitting without touching the threads.
A joint sealing compound or tape should not be used on the flare fitting’s threads when it is finally installed. To make joining your fitting simpler, use a drop of threading oil. Always do a leak test after making a new connection; this is especially important when working with gas or oil lines.